Astronauts will face a host of obstacles when they visit the Moon again. There’s powerful radiation, wild temperature swings, and challenging gravity to deal with. There’s also dust and lots of it. Moondust was a hazard for the Apollo astronauts, and future lunar astronauts will have to contend with it, too.
What if they turn some of that dust into solid surfaces to drive on?
When Apollo 11 was preparing for the first Moon landing, they faced a lot of unknowns. They knew from orbital images that there was a lot of dust, but mission planners didn’t know how much or how deep. There was a risk of sinking into it. So serious was the risk that the lander had three dust-sensing probes extending downward from three of the lander’s feet. If they sank too deeply into dust, the landing could be aborted.
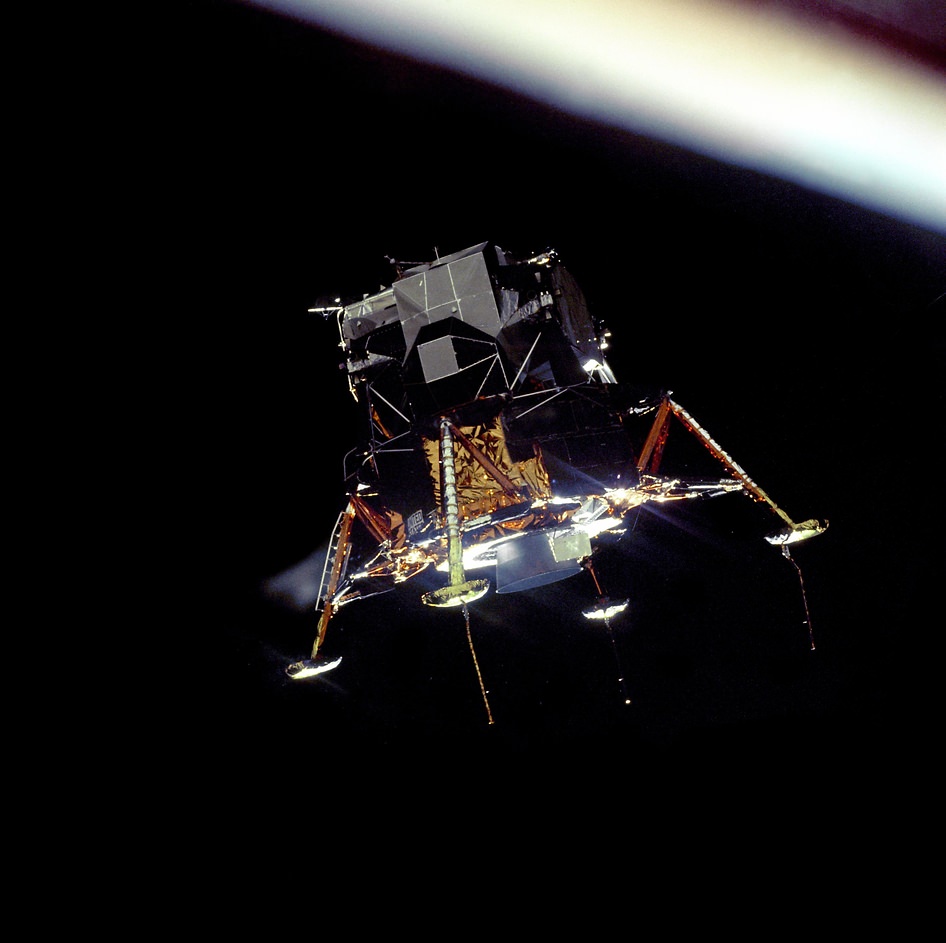
They didn’t sink in, as we all know, but the dist did cause problems, and the Apollo astronauts weren’t on the lunar surface for very long.
Since then, we’ve learned a lot about lunar dust and the obstacles it imposes on exploration. The ESA will eventually establish a sustained human presence on the Moon so that our natural satellite can be more fully explored. Eventually, in-situ resource development will form part of the mission.
All that activity means the astronauts will need transportation, reliable transportation that lasts a long time. And that means somehow dealing with the fine, clinging dust that coats the Moon. Rather than engineer surface vehicles that are somehow impervious to dust, the ESA thinks they can melt the dust where it sits, forming a hardened driving surface. Will that solve the problem?
NASA modelling shows that when a spacecraft touches down on the lunar surface, it can send tons of fine dust above the surface before eventually settling. Due to the Moon’s low gravity, it can take a long time to settle. That wasn’t a huge problem for Apollo’s small landers, but future landers will be much larger. All that dust could foul the surfaces of landers and cause all kinds of problems. But what if the dust on landing areas and travelling surfaces could be melted with high-energy lasers?
The ESA decided this is a tactic worth pursuing. Their PAVER (paving the road for large area sintering of regolith) program investigated the idea. PAVER is a consortium of European companies and organizations. In controlled tests on simulated lunar regolith, they used a 12-kilowatt CO2 laser to melt simulated moondust. It created a smooth, glassy surface that has potential as roadways, landing areas, and other operational areas from the Moon’s plentiful dust.
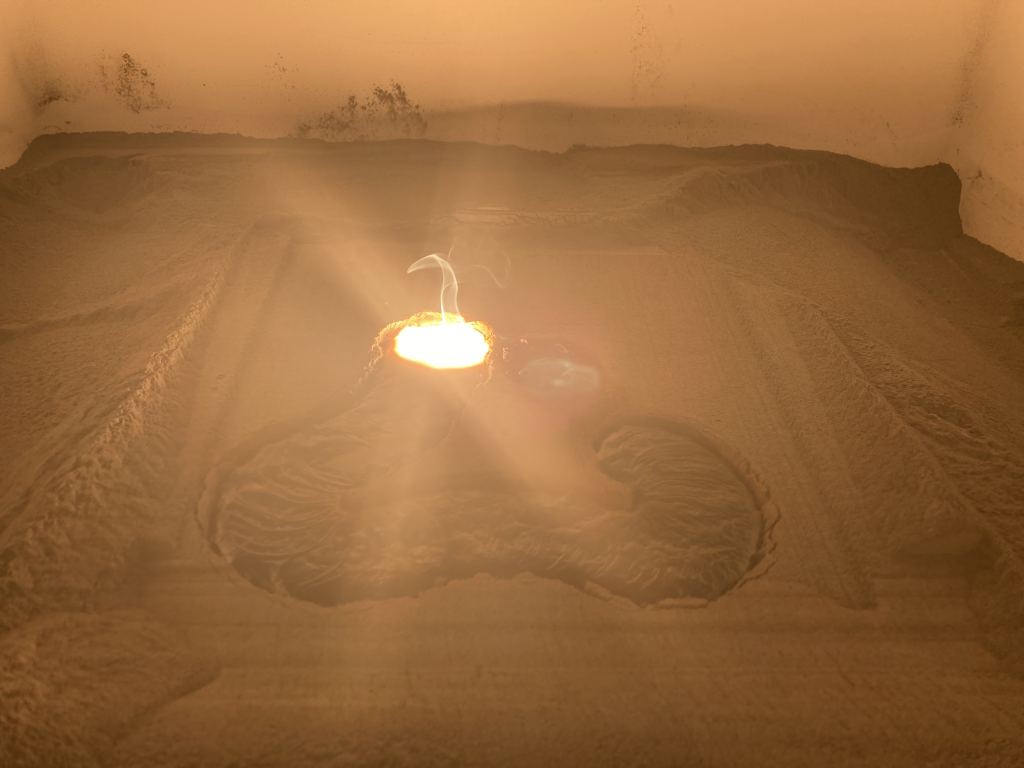
This idea has a history. Back in 1933, there was a proposal to melt Earthly sand into a solid driving surface. The idea appeared in Modern Mechanix. It didn’t involve lasers, of course. Instead, it would use a lens to focus the Sun’s energy.
The idea never took off for various reasons. But on the Moon, in-situ resource exploitation is critical to success. We won’t be manufacturing any asphalt and laying it down. Could laser sand work there?
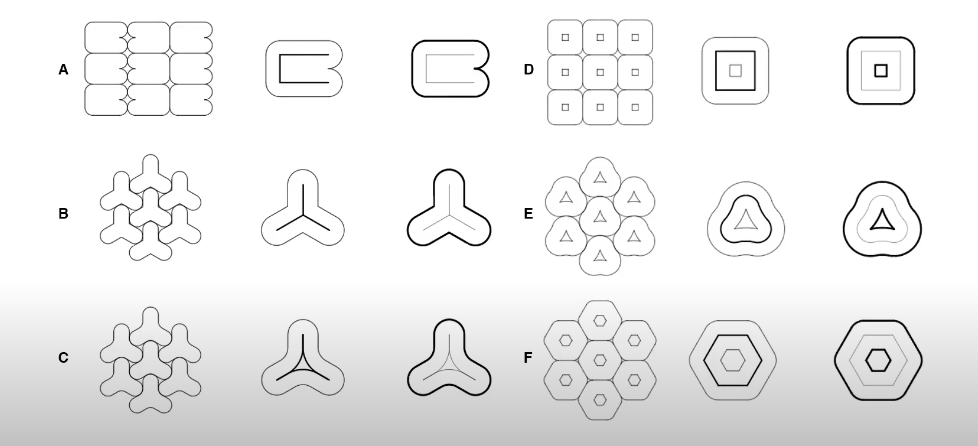
“In practice, we would not bring a carbon dioxide laser on the Moon,” said ESA Materials Engineer Advenit Makaya. “Instead, this current laser is serving as a light source for our experiments to take the place of lunar sunlight, which could be concentrated using a Fresnel lens a couple of metres across to produce equivalent melting on the surface of the Moon.”
A Fresnel lens is more compact than other lenses and uses less material. They were developed for use in lighthouses in the 18th century. They were called the “invention that saved a million ships.” Maybe on the Moon, this relatively simple technology can help our modern-day explorers.
A new paper in Nature Scientific Reports presented the PAVER results in more detail. It’s “Laser melting manufacturing of large elements of lunar regolith simulant for paving on the Moon.” The first author is Juan-Carlos Ginés-Palomares, Assistant Researcher at the Technical University in Berlin.
“Looking at raw material and energy, solar energy and lunar regolith are directly available on the Moon, meaning that the direct sintering or melting of the regolith is a feasible approach for the manufacturing of objects on the lunar surface,” the paper states. “Mobile solutions such as solar or laser energy sources can be used to manufacture roads or landing pads in situ.”
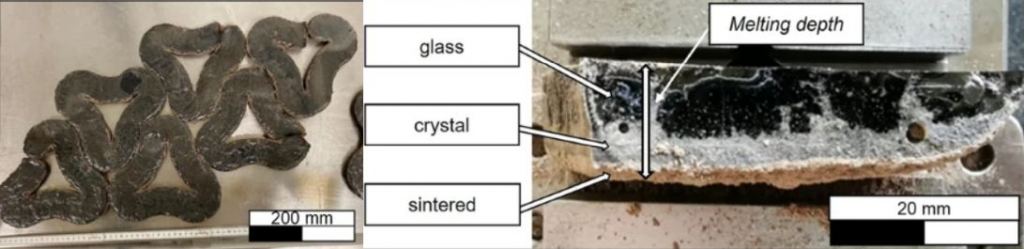
The researchers examined their samples with a scanning electron microscope for cracks, bubbles, and the presence of microcrystals and nanocrystals. They also tested their samples to see how much pressure they can withstand. High compression strength is obviously a critical characteristic of a road surface. They found that their samples had varied compressive strengths from 216.29 to 56.19 MPa, with a mean of 93.97 MPa. Concrete typically has a compressive strength in the range of 20–120 MPa, though it varies widely depending on formulation.
In-situ resource utilization using the Sun is a hot topic, and researchers have studied different ways of building infrastructure out of lunar regolith using the Sun’s energy. But this research expanded the footprint of the materials being formed.
“During past in-situ resource utilization projects – including brick building using mirror-concentrated solar heat – we’ve been looking at surface melting limited to relatively small melt spots, from a few millimetres to a couple of centimetres in diameter,” Makaya said. “For building roads or landing pads, a much wider focal point is required to be able to scan a very wide area in a practical timescale.”
Driving around on the Moon is much different than on Earth. There’s no rain and no moisture to create problematic freeze-thaw cycles. There’s minimal traffic, much less weight, and likely no accidents. So, the only real strain on the laser roads would be downward.
“The resulting material is glasslike and brittle but will mainly be subject to downward compression forces,” said Makaya. “Even if it breaks, we can still go on using it, repairing it as necessary.”
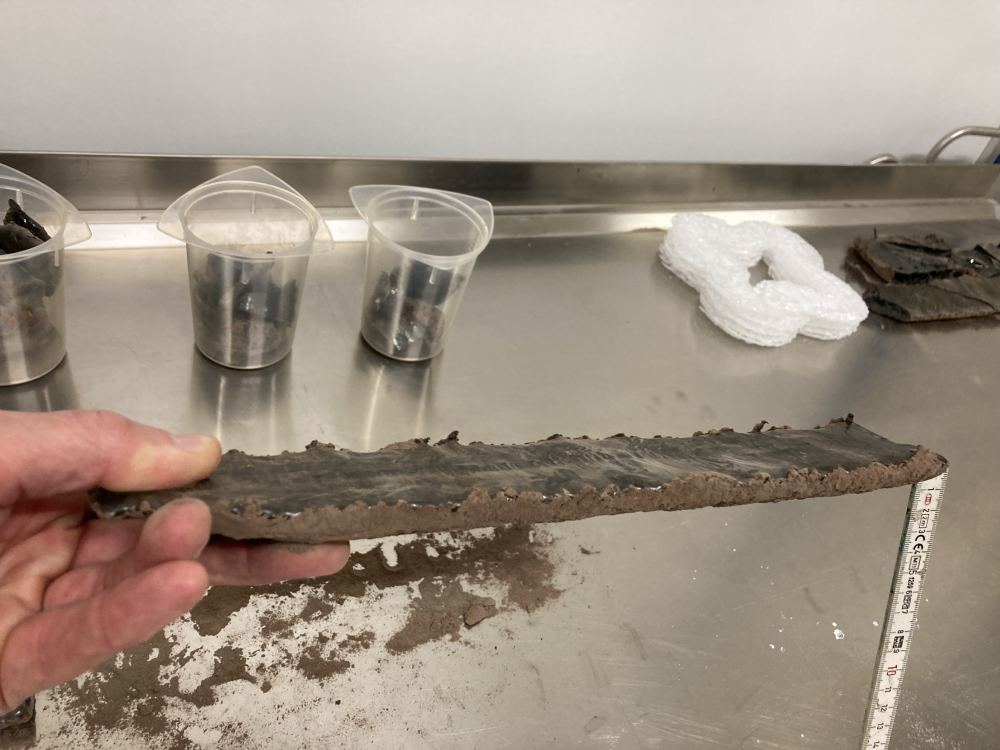
The method is time-consuming, but so is everything on the Moon. A 100 sq. m landing pad with a thickness of 2 cm of dense material might be constructed in 115 days, according to the researchers.