Orion EFT-1 heat shield is off loaded from NASA’s Super Guppy aircraft after transport from Manchester, N.H., and arrival at the Kennedy Space Center in Florida on Dec. 5, 2013. Credit: Ken Kremer/kenkremer.com
Story updated[/caption]
KENNEDY SPACE CENTER, FL – The heat shield crucial to the success of NASA’s 2014 Orion test flight has arrived at the Kennedy Space Center (KSC) aboard the agency’s Super Guppy aircraft – just spacious enough to fit the precious cargo inside.
Orion is currently under development as NASA’s next generation human rated vehicle to replace the now retired space shuttle. The heat shields advent is a key achievement on the path to the spacecraft’s maiden flight.
“The heat shield which we received today marks a major milestone for Orion. It is key to the continued assembly of the spacecraft,” Scott Wilson, NASA’s Orion Manager of Production Operations at KSC, told Universe Today during an interview at the KSC shuttle landing facility while the offloading was in progress.
“It will be installed onto the bottom of the Orion crew module in March 2014.”
The inaugural flight of Orion on the unmanned Exploration Flight Test – 1 (EFT-1) mission is scheduled to blast off from the Florida Space Coast in mid September 2014 atop a Delta 4 Heavy booster, Wilson told me.
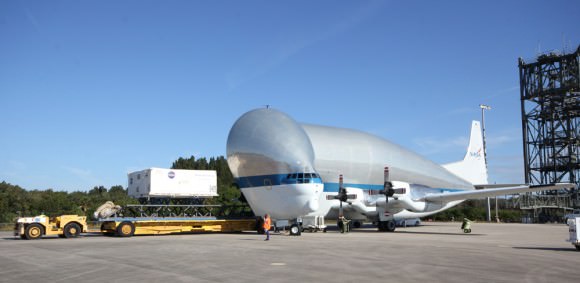
The heat shield was flown in from Textron Defense Systems located near Boston, Massachusetts and offloaded from the Super Guppy on Dec. 5 as Universe Today observed the proceedings along with top managers from NASA and Orion’s prime contractor Lockheed Martin.
“The Orion heat shield is the largest of its kind ever built. Its wider than the Apollo and Mars Science Laboratory heat shields,” Todd Sullivan told Universe Today at KSC. Sullivan is the heat shield senior manager at Lockheed Martin.
The state-of-the-art Orion crew capsule will ultimately enable astronauts to fly to deep space destinations including the Moon, Asteroids, Mars and beyond – throughout our solar system.
The heat shield was one of the last major pieces of hardware needed to complete Orion’s exterior structure.
“Production of the heat shields primary structure that carries all the loads began at Lockheed Martin’s Waterton Facility near Denver,” said Sullivan. The titanium composite skeleton and carbon fiber skin were manufactured there to give the heat shield its shape and provide structural support during landing.
“It was then shipped to Textron in Boston in March,” for the next stage of assembly operations, Sullivan told me.
“They applied the Avcoat ablater material to the outside. That’s what protects the spacecraft from the heat of reentry.”
Textron technicians just completed the final work of installing a fiberglass-phenolic honeycomb structure onto the heat shield skin. Then they filled each of the honeycomb’s 320,000 cells with the ablative material Avcoat.
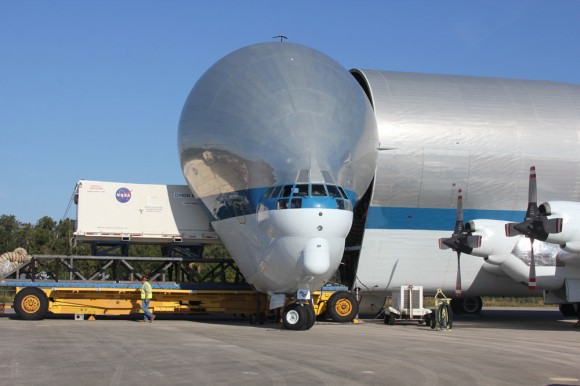
Each cell was X-rayed and sanded to match Orion’s exacting design specifications.
“Now we have about two and a half months of work ahead to prepare the Orion crew module before the heat shield is bolted on and installed,” Sullivan explained.
The Avcoat-treated shell will shield Orion from the extreme heat of nearly 4000 degrees Fahrenheit it experiences during the blazing hot temperatures it experiences as it returns at high speed to Earth. The ablative material will wear away as it heats up during the capsules atmospheric re-entry thereby preventing heat from being transferred to the rest of the capsule and saving it and the human crew from utter destruction.
“Testing the heat shield is one of the prime objectives of the EFT-1 flight,” Wilson explained.
“The Orion EFT-1 capsule will return at over 20,000 MPH,” Wilson told me. “That’s about 80% of the reentry speed experienced by the Apollo capsule after returning from the Apollo moon landing missions.”
“The big reason to get to those high speeds during EFT-1 is to be able to test out the thermal protection system, and the heat shield is the biggest part of that.”
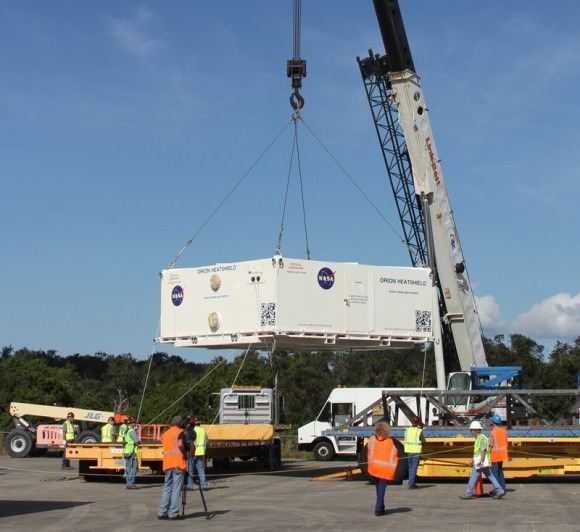
The two-orbit, four- hour EFT-1 flight will lift the Orion spacecraft and its attached second stage to an orbital altitude of 3,600 miles, about 15 times higher than the International Space Station (ISS) – and farther than any human spacecraft has journeyed in 40 years.
“Numerous sensors and instrumentation have been specially installed on the EFT-1 heat shield and the back shell tiles to collect measurements of things like temperatures, pressures and stresses during the extreme conditions of atmospheric reentry,” Wilson explained.
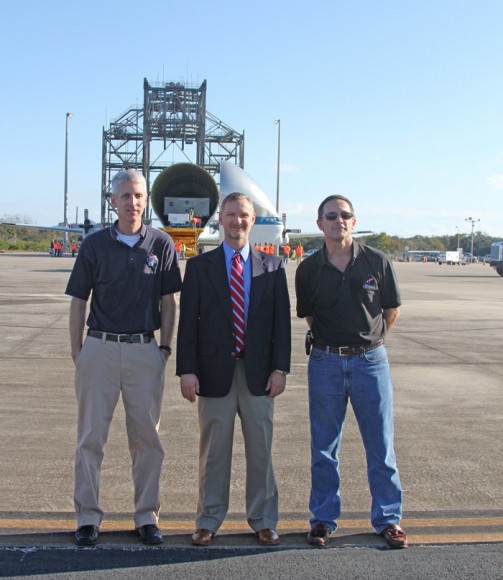
The data gathered during the unmanned EFT-1 flight will aid in confirming. or refuting, design decisions and computer models as the program moves forward to the first flight atop NASA’s mammoth SLS booster in 2017 on the EM-1 mission and human crewed missions thereafter.
“I’m very proud of the work we’ve done, excited to have the heat shield here [at KSC] and anxious to get it installed,” Sullivan concluded.
Stay tuned here for continuing Orion, Chang’e 3, LADEE, MAVEN and MOM news and Ken’s reports from on site at Cape Canaveral & the Kennedy Space Center press site.
…………….
Learn more about Orion, MAVEN, MOM, Mars rovers, Chang’e 3, SpaceX, and more at Ken’s upcoming presentations
Dec 10: “Antares ISS Launch from Virginia, Mars and SpaceX Mission Update”, Amateur Astronomers Association of Princeton, Princeton University, Princeton, NJ, 8 PM
Dec 11: “Curiosity, MAVEN and the Search for Life on Mars”, “LADEE & Antares ISS Launches from Virginia”, Rittenhouse Astronomical Society, Franklin Institute, Phila, PA, 8 PM
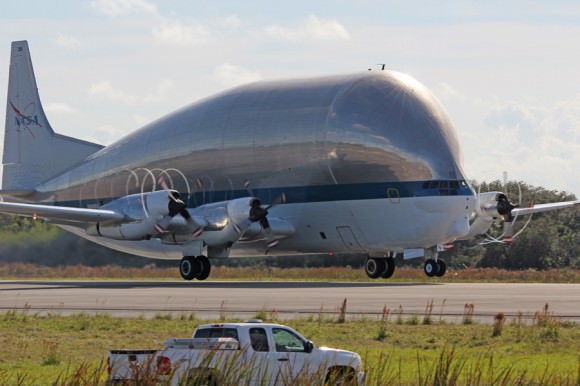