When it comes time for NASA to send astronauts back to the Moon and on to Mars, a number of new spacecraft systems will come into play. These include the Space Launch System (SLS), the most powerful rocket ever built, and the Orion Multi-Purpose Crew Vehicle (MPCV) – a next-generation spacecraft that will carry crews beyond Low Earth Orbit (LEO).
Naturally, before either of these systems can conduct missions, extensive testing needs to be conducted to ensure they are safe and will perform well. In this spirit, NASA Advanced Supercomputing (NAS) research scientists are currently conducting highly-detailed simulations and visualizations to ensure that the Orion spacecraft’s Launch Abort Vehicle (LAV) will keep crews safe, should an emergency occur during takeoff.
Basically, the LAV is the combined configuration of the Orion Launch Abort System (LAS) and crew module, and is designed to get the crew to safety if an emergency occurs on the launch pad or during the first two minutes of flight. These simulation and visualization techniques, which were conducted with the Pleiades supercomputer at the NASA Ames Research Center, predict how vibrations will affect the Orion spacecraft’s launch abort vehicle during takeoff.
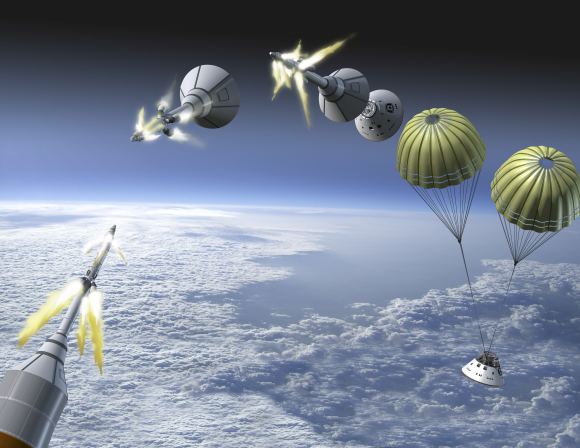
Not only are these tests assisting with the design efforts of the Orion LAV motor (a collaborative effort between NASA and Orion prime contractor Lockheed Martin), they are also rather unprecedented as far as spacecraft development goes. As Francois Cadieux, a research scientist in the NAS Computational Aerosciences Branch, explained:
“This is one of the first times where large eddy simulation (LES) techniques have been used in full-scale spacecraft analysis and design at NASA. I’m excited to play a part in the agency’s next big human space exploration project—this work brings LES to a point where it can provide accurate predictions within a short enough turnaround time to guide Orion’s design.”
Previously, the use of such high-fidelity tools has been largely restricted to academic research, and not something private industry contractors could take advantage of. Together with Michael Barad – an aerospace engineer at the Ames Research Center – Cadieux produced a variety of turbulence-resolving computational fluid dynamics (CFD) simulations using the NAS-developed Launch Ascent and Vehicle Aerodynamics (LAVA) software.
They were assisted by NAS visualization experts, who helped the researchers identify different types of vortices that can caused noise and vibrations. Using this simulation data, the visualization experts created a series of high-quality images and movies that illustrated what kind of flow dynamics the Orion LAS would experience during a launch abort. As Cadieux explained:
“From these visualizations, we were able to identify areas of high vibrational loads on the vehicle, and their sources. What we learned is that noise coming from the turbulence of the plume is substantially higher than any noise generated from its interaction with attached shockwaves.”
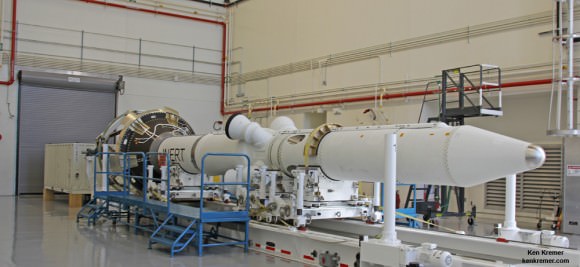
The video below shows the simulation of an ascent abort scenario, where the LAS has detached from the SLS and is traveling at close to the speed of sound. The abort process initiates with the ignition of the LAS motor and then slows down as the pressure and airflow conditions become particularly harsh.
The colored plumes indicate high pressure (red) and low pressure (blue), with pixels changing from blue to red (and vice versa) in relation to pressure waves that cause vibrations on the vehicle (white). The regions where the color changes abruptly, but remains generally blue or red over time, indicates the presence of shock waves. In the end, these simulations are directly impacting the spacecraft’s design and will help ensure astronaut safety and spacecraft performance.
“We’re still asking lots of questions,” said Cadieux. “Like, how do the loads on the LAV surface change at higher angles of attack? How do we best use data from wind tunnel tests to predict loads for actual flight conditions where the vehicle is accelerating?”
The answers to these questions will will be used to design the next series of ground tests, crew mockup tests, and critical flight tests, which will will prepare the Orion spacecraft for its first crewed mission – Exploration Mission 2 (EM-2). This mission, which is scheduled for launch by 2023, will consist of four crew members conducting a lunar flyby and delivering the first components for the Deep Space Gateway.
Be sure to check out the simulation video as well, courtesy of the NASA Ames Research Center: